Search by Solution or Feature
Lifting and Bulging
Issue and Concerns
General pressure-sensitive adhesives tend to lift or bulge when exposed to high temperatures, yet these adhesives are used in many places frequently exposed to high temperatures.
*Can be scrolled horizontally
Examples | Issue occurrence |
---|---|
Inside cars in the summertime and around engines | The tape that binds the decorations around the dashboard and cords around the engine peels off |
Outer side of car doors | Decorations on the outside of car doors peel off |
Securing electronic parts | Product defects occur due to malfunctioning electronic devices or parts |
Securing aircraft and satellite components | Satellites become inoperable |
Mirror film for ceiling insulation | Mirror film can start to lift, resulting in poor appearance |
Thus, heat resistance is a very important quality in contexts where heat is applied to the material.
Causes of Lifting and Bulging
Many automobile interiors and electronic device parts are made of plastic and other resin materials, and outgassing from this plastic can cause adhesive tape to lift and bulge.
Impact of Outgassing
Resin panels made from plastics such as polycarbonate and ABS readily absorb moisture, and at high temperatures, gases (bubbles) are released from the resin.
The Soken Solution
Heat and foam resistance are needed to eliminate lifting and bulging. The interior of a car can get very hot in the summer, so heat resistance is a necessary property to deal with this. Incorporating foam resistance into the material to control outgassing can eliminate lifting and bulging.
Among our products, SK Dyne™ 1838 is equipped with heat and foam resistance.
What is heat resistance in the context of pressure-sensitive adhesives?
General pressure-sensitive adhesives are easily warped and peel off when exposed to heat. Heat-resistant pressure-sensitive adhesives remain unchanged or change very little when exposed to heat compared to normal conditions.
Evaluation Methods
Our evaluation methods are introduced on our page about the basic properties of pressure-sensitive adhesives.
High-Temperature Adhesive Strength Test
What is adhesive strength?
In the adhesive strength test, we measure the force it takes to peel the material off the adherend to evaluate how difficult it is to remove.
For example, when peeling tape off a cardboard box, you might ask, “How much force do I need to peel this off?” The answer is the adhesive strength of the tape.
The higher the value, the more firmly it is attached to the adherend.
Adhesive strength strongly depends on the temperature at the time of measurement and the properties of the adherend material.
Adhesive strength testing is generally conducted at room temperature (25°C). However, this test is conducted under harsh conditions from 80°C to 120°C to determine whether changes in adhesive strength are observed at high temperatures.
The adhesive strength of general products decreases from 100°C to 120°C as the test environment becomes more harsh. At 120°C, their adhesive strength is approximately 10% of that at 80°C. SK Dyne™ 1838, on the other hand, does not lose adhesive strength as rapidly as general products with increasing temperatures. Even at 120°C, its adhesive strength holds at approximately 40% of its strength at 80°C; this is about four times the adhesive strength of general products at 120°C.
There is little change in the decrease in adhesive strength after heat treatment, indicating that the pressure-sensitive adhesive is able to withstand heat without warping, even at high temperatures.
High-temperature adhesive strength
- ●Test conditions
- Substrate: 125 μm PET film
Coating thickness: 30 μm
Adherend: Polycarbonate/ABS alloy
Peel angle: 180°
Peel speed: 200 mm/min
Sample width: 25 mm
Heating time: 10 min
Heat Resistance Holding Power Test
What is holding power?
To test holding power, a fixed weight is applied to adhesive tape for a specific amount of time. The distance that the tape moves in this time is used to evaluate the material's resistance to slipping.
The smaller the number, the more resistant the tape is to move, indicating it is “anti-slip tape.”
Additionally, the only place in the tape that is warped is the pressure-sensitive adhesive layer.
The thicker the tape, the more the pressure-sensitive adhesive layer increases, which generally reduces the ability of the tape to resist slipping.
In this test, a 1 kg weight is placed on the tape at a temperature of 80°C, and the amount of slipping is measured after one hour. The evaluation was carried out using varying thicknesses of pressure-sensitive adhesive from 10 to 30 μm.
The tape on the adherend showed no displacement (0 mm after one hour), which did not change even as the thickness was varied.
Due to its high holding power, the pressure-sensitive adhesive does not change even when subjected to heat, indicating extremely high performance.
- ●Test conditions
- Substrate: 25μm PET
Adherend: Stainless steel (SUS)
Attached area: 20 x 20 mm2
Test duration: 1 hour
Weight: 1 kg
Ambient temperature: 80°C
Thickness of adhesive layer [μm] |
10 | 20 | 30 |
---|---|---|---|
Amount of displacement after one hour [mm] |
0 | 0 | 0 |
Heat-Induced Bubbling Resistance Test
In this test, the adhesive tape is affixed to a plastic panel. As a pretreatment, an autoclave (pressure application treatment) removes the air from the adherend when the tape is applied, enabling complete attachment to the surface. After enduring 24 hours in a high-temperature test environment at 120°C, the product is visually evaluated for the presence of bubbles.
While general products are unable to suppress outgassing, causing bubbles to form and resulting in lifting and bulging, SK Dyne™ 1838 has high adhesion to plastics, making it highly resistant to outgassing and thus preventing those issues.
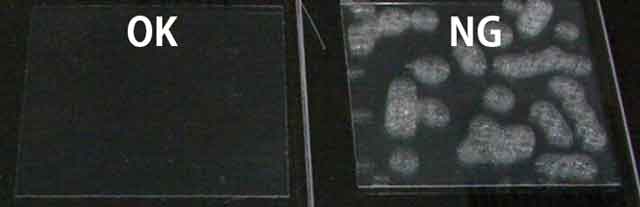
- ●Test conditions
- Substrate: 125 μm PET film
Coating thickness: 30 μm
Adherend: Polycarbonate
Heating conditions: 24 hours at 120°C
Attaching conditions: Attached under 23°C-50% RH conditions and autoclaved (50°C, 5 kg/cm2 for 20 min) for adhesion.
SK Dyne™ 1838
Expected Applications
- Anti-reflection films
- Dashboard decorations
- Anti-shattering films
- Decorations for the back of smartphones
- Uses with polycarbonates
Examples: game consoles, dryers, computers, digital cameras, irons, globe light bulbs, automobile headlamp lenses, door handles, motorcycle windshields, tail lamps, carports
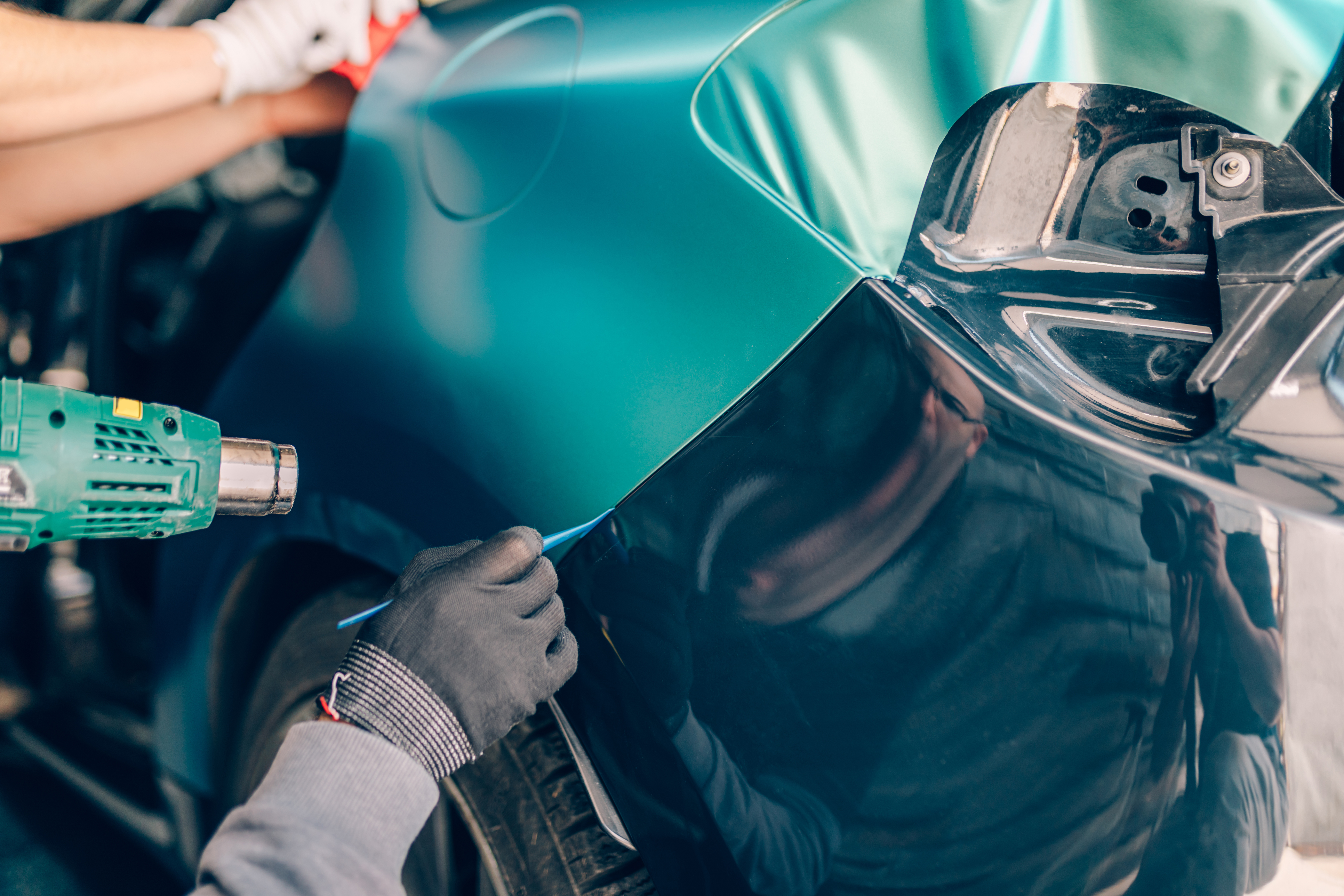
Peeling
Issue and Causes
Adhesive tape peeling is a combination of many different factors. While the compatibility between the pressure-sensitive adhesive and the adherend (the material the adhesive is stuck to) is important, we will explain three other important factors here.
Peeling on curved surfaces:
When the adherend is curved and complex in shape, such as with automobile interior parts, the resilience of the substrate causes the adhesive to want to return to its original shape, making it easier to peel off than flat surfaces. This is especially true when the adherend is made of hard-to-adhere materials (difficult to stick).
Peeling due to heat and vibrations:
When used on areas that constantly vibrate or generate heat, such as smartphones, the product may not operate properly if peeling occurs.
Peeling due to thinning:
In general, adhesive strength tends to be higher with a thicker film within a certain range, while a thinner adhesive layer is more vulnerable to impacts and resultant peeling.
*Can be scrolled horizontally
Context | Examples |
---|---|
Peeling on curved surfaces | Automobile interior parts (door lining and roof) Wire harnesses, pillar posters, air conditioning piping, drainage hose repairs, etc. |
Peeling due to heat and vibrations | Electronic parts, computer display parts, washing machines (buttons) |
Peeling due to thinning | Anti-shattering films for electronic displays of devices such as smartphones, tablets, and TVs |
Lighter and thinner backlight frames for electronic devices like smartphones and tablets |
Basic Properties of Pressure-Sensitive Adhesives
Peeling on curved surfaces
Causes of peeling
The objects to which adhesive sheets and tapes are attached have various shapes ranging from level to curved. Adhesives tend to peel more easily off curved surfaces due to the tendency of the substrate to want to return to its original shape. In addition, many hard-to-adhere materials, such as olefins, have insufficient stress mitigation properties, resulting in peeling.
The Soken Solution
SK Dyne™ 1701DT, with its high olefin adhesion and stress mitigation capabilities, can eliminate peeling.
What is curved surface repulsion?
Curved surface repulsion is the force that tries to restore the substrate to its normal shape when bent. Pressure-sensitive adhesives with excellent stress resistance can firmly adhere to the adherend while withstanding the repulsive force of its substrate.
Curved Surface Repulsion Test
The curved surface repulsion test evaluates how well the pressure-sensitive adhesive can withstand the force that tries to revert the substrate to its original shape when applied to a curved surface. Since tapes with foam substrates are often used for applications on curved surfaces, this test involves attaching a foam substrate tape to a polypropylene cylinder and evaluating whether the tape peels off after 24 hours at 80°C. Curved surface adhesion means that the foam tape remains firmly attached to the polypropylene cylinder without peeling off over time.
SK Dyne™ 1701DT, with its superior adhesion to olefins and stress resistance, can be applied to curved surfaces.
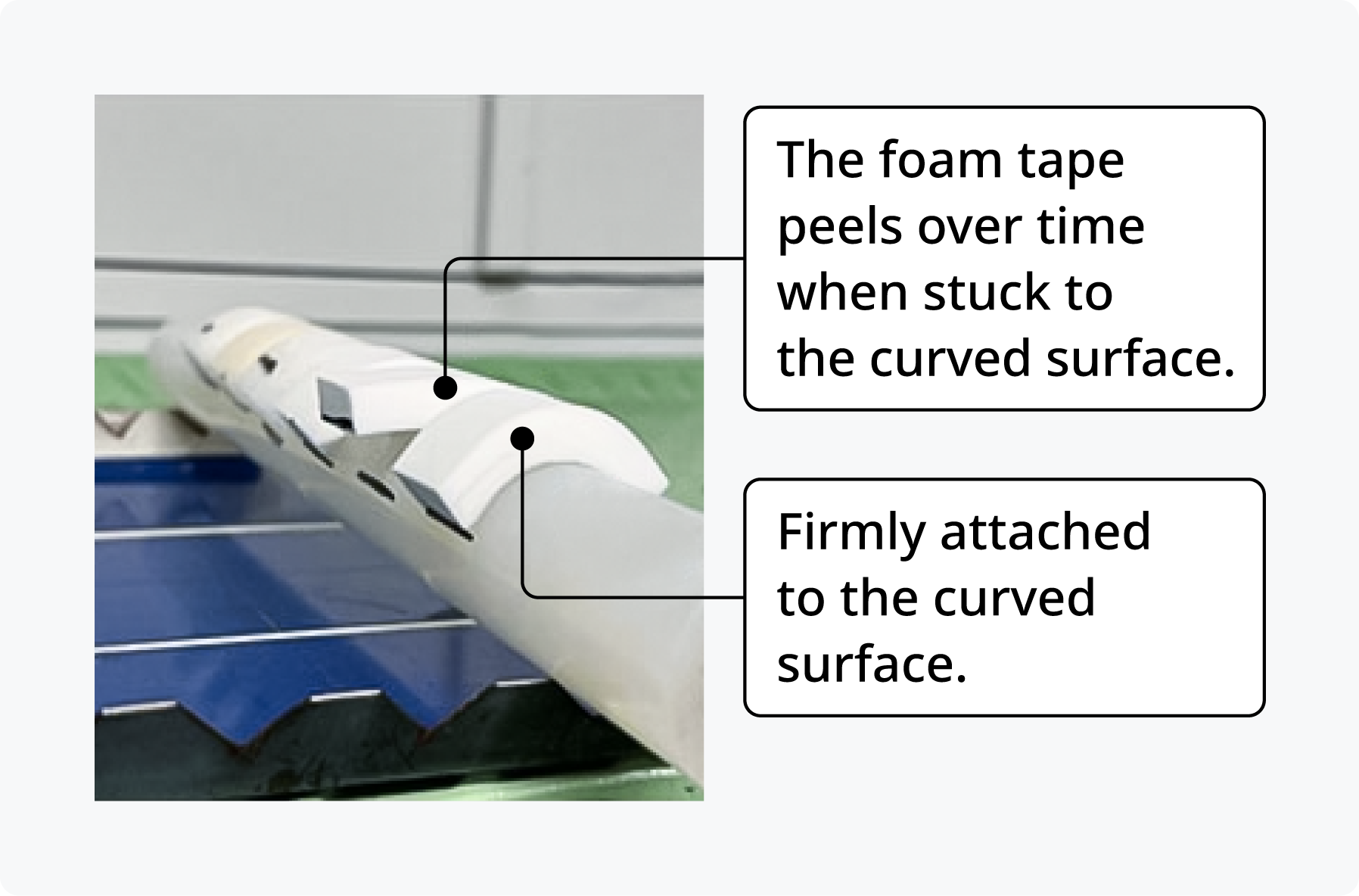
Adhesive Strength Comparison Test
Adhesive strength varies greatly depending on the material of the adherend to which it is attached. This adhesion test is performed separately on stainless steel and polycarbonate panels. Polycarbonate is widely used in automobile interior parts and other environments that can experience high temperatures. As such, evaluations were carried out at 80°C. The stainless steel panels were done at room temperature. We have also compared how the adhesive strength changes for general products and SK Dyne™ 1701DT when the pressure-sensitive adhesive thickness varies.
Test results show that SK Dyne™ 1701DT has approximately 1.6 times the adhesive strength of general products at 10 μm on one side, which is equivalent to the adhesive strength of general products at a thickness of 30 μm. Double-sided tapes obtained similar results, indicating that SK Dyne™ 1701DT performs extremely well with thin films and at high temperatures.
- ●Test conditions
- Adherend: Stainless steel (SUS) / Polycarbonate (PC)
Sample width: 25 mm
Sample composition: One-sided pressure-sensitive adhesive layer of 10/20/30 μm / PET substrate 25 μm
Double-sided pressure-sensitive adhesive layer of 10/30 μm / PET core material 25 μm / Pressure-sensitive adhesive layer of 10/30 μm / PET substrate 25 μm Peel angle: 180°
Peel speed: 300 mm/min
Measurement conditions: 23°C (SUS) / 80°C (PC)
Compress conditions: 2 kg roller, 3 rolls back and forth
Curing conditions: 23°C, 50% RH
*Can be scrolled horizontally
Adherend | Adhesive layer (μm) | Adhesive strength (N/25mm) | |
---|---|---|---|
General products | 1701DT | ||
SUS | 25 | 12.2 | 14.0 |
PC (80℃) |
10 | 10.5 | 16.7 |
20 | 14.7 | 19.2 | |
30 | 16.7 | 23.1 | |
Double-sided 10,10 | 10.3 | 15.1 | |
Double-sided 30,30 | 16.6 | 23.8 |
Peeling due to heat and vibrations
Causes
Tapes for securing electronic components come in various shapes and sizes, and insufficient heat or stress resistance can cause them to peel.
The Soken Solution
Electronic devices such as smartphones tend to get hot when used for long periods of time due to the buildup of internal heat. Demand has emerged for adhesives that can maintain their adhesive strength even when subjected to heat to deal with situations like these. Stress mitigation properties of the pressure-sensitive adhesive are also important to ensure that it can withstand the shock of a device being dropped and the vibration of electrical appliances.
In such situations, SK Dyne™ 1701DT, with its high heat and stress resistance, can eliminate peeling issues.
Fixed Load Peel Test
In the fixed load peel test, an adhesive tape is applied to an adherend, held horizontally, and a load is applied under the tape to evaluate its resistance to peeling. The smaller the peeling distance, the more resistant the adhesive tape is when a load is applied to it, and the more difficult it is to peel. Stress is generated when a load is applied to the edge of the adhesive tape, and if the tape cannot withstand this stress, it may peel off the adherend. Fixed load peel force is greatly affected by the temperature at which the test is conducted, the adherend material, and the adhesive layer's thickness. As such, this test applies a load to the tape at a temperature of 80°C and evaluates how much the tape peels off after one hour. The evaluation was conducted on stainless steel and polypropylene panels, varying the pressure-sensitive adhesive thickness from 10 to 30 μm.
The test results showed that SK Dyne™ 1701DT was difficult to peel even at 80°C. In particular, on the polypropylene panels, while all the general products completely peeled and fell, SK Dyne™ 1701DT only peeled a very small distance of 1 to 3 mm after 1 hour. SK Dyne™ 1701DT exhibits excellent stress mitigation properties, sticking tightly to both stainless steel and polypropylene plates and making it difficult for the tape to peel.
What is stress mitigation?
Stress is the internal force generated inside a part when subjected to an external force.
When removing adhesive tape, stress is generated within the pressure-sensitive adhesive. If a certain amount of force is applied to the tape, it will warp and become easier to peel. Pressure-sensitive adhesives that excel in stress mitigation can resist the forces that cause peeling, ensuring a firm and lasting bond.
- ●Test conditions
- Adherend: Stainless steel (SUS) / Polypropylene (PP)
Adhered area: 20 x 50 mm2
Load: 100 g (80°C SUS) / 50 g (80°C PP)
Compress conditions: 2 kg roller, 3 rolls back and forth
Curing conditions: 23°C, 50% RH for 1 hour
*Can be scrolled horizontally
Adherend | Adhesive layer (μm) | Peeling (mm) / ↓ Falling (min) | |
---|---|---|---|
General products | 1701DT | ||
SUS (80℃) |
10 | 22'↓ | 3 |
20 | 34 | 0 | |
30 | 16 | 0 | |
PP (80℃) |
10 | 10'↓ | 3 |
20 | 18'↓ | 1.5 | |
30 | 37'↓ | 1 |
SK Dyne™ 1701DT
Expected Applications
- Securing the area around displays of devices such as smartphones and TVs
- Securing electronic components and modules and their parts to each other
- Control panels and switches for washing machines
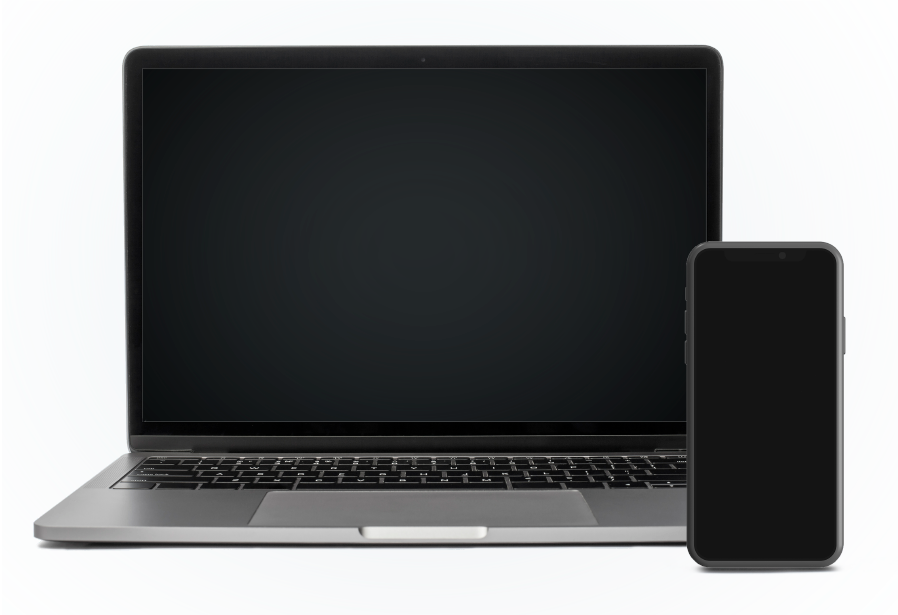
Peeling due to thinning
Causes
As electronic devices such as smartphones, tablets, and TVs become thinner, their adhesive sheets must also become thinner. While decreasing pressure-sensitive adhesive usage by applying a thinner layer cuts costs and saves energy, a small adhesive layer decreases adhesive strength and can lead to peeling.
In the context of electronic displays, many products are designed for high elasticity to prevent surface flaws like dents. However, this can lead to a reduction in adhesive strength, which in turn may become a primary factor contributing to peeling. Another cause of peeling is insufficient adhesive strength due to a lack of compatibility with the adherend.
The Soken Solution
For situations where thinner films are needed, SK Dyne™ 1838 and SK Dyne™ 1515DT are two suitable choices depending on the adherend material and specific application.
SK Dyne™ 1838 | Anti-scattering film application for electronic displays8
SK Dyne™ 1838 is colorless, transparent, and suitable for applications requiring visibility and is expected to be used for optical films, glass, and other similar applications. To prevent peeling in thin films, the adhesive needs to maintain strong adhesion to glass, even at thicknesses of 10 μm or less, ensuring no peeling occurs despite the reduced thickness. Enhancing adhesion to glass can be a solution to the issues with thin films.
- * SK Dyne™ 1838 is also available in an environmentally friendly version.
SK Dyne™ 1515DT | Applications for electronic devices
As electronic devices become thinner, so do their internal components. We expect a demand for adhesive tapes with thinner films to secure these thinner electronic components. SK Dyne™ 1515DT is the most adhesive product in our lineup and does not peel even when applied as a thin double-sided film. It is suitable for electronic components and other applications where thinness and adhesive strength are required and can eliminate the problem of peeling.
Illustration of peeling when thinned
Thinning indicates a decrease in the adhesive layer, as shown in the figure. Since the pressure-sensitive adhesives suppress the force to peel it off with the entire layer, adhesive strength decreases as the layer is thinned. Thinned tapes are more likely to lose adhesiveness and peel when subjected to shock from being dropped or some other source.
Adhesive Strength Comparison Test (Glass)
In this test, adhesive strength is evaluated by applying the tape to two types of adherends: "alkali glass," which is a common general-use glass, and "alkali-free glass," which does not contain alkaline components and is used as a substrate material for displays due to its superior chemical resistance. The AC tape is autoclaved (pressure-treated) to remove air at the time of lamination to ensure complete adhesion to the adherend.
Test results show that SK Dyne™ 1838 has higher adhesive strength to glass and is more difficult to peel off compared to general products. This adhesive is designed with high elasticity and adhesive strength to prevent denting.
- ●Test conditions
- Adherend: Glass (alkali / alkali-free)
Sample width: 25 mm
Sample composition: 25µm pressure-sensitive adhesive layer / 50µm PET substrate
Film thickness: 25 μm
Substrate: 50 μm PET
Peel angle: 180°
Peel speed: 300 mm/min
Curing conditions: 23°C, 50% RH
Compress conditions: 2 kg roller, 3 rolls back and forth
(with AC: 70°C x 5 atm x 30 min)
*Can be scrolled horizontally
Adherend | Adhesive strength (N/25mm) | ||
---|---|---|---|
General products | 1838 | ||
Glass | Alkaline No AC | 17.6 | 20.8 |
Alkaline No AC | 20.0 | 23.9 | |
Alkali-free AC | 20.4 | 26.6 |
SK Dyne™ 1838
Expected Applications
As a solution to thinning:
- Anti-scattering film and optical film applications for electronic displays
As a glass adhesive:
- Automotive film antennas
- Securing ETC antennas and dashcams
- Labels on glass
- Films for glass decorations
- Other applications requiring strong adhesion to glass
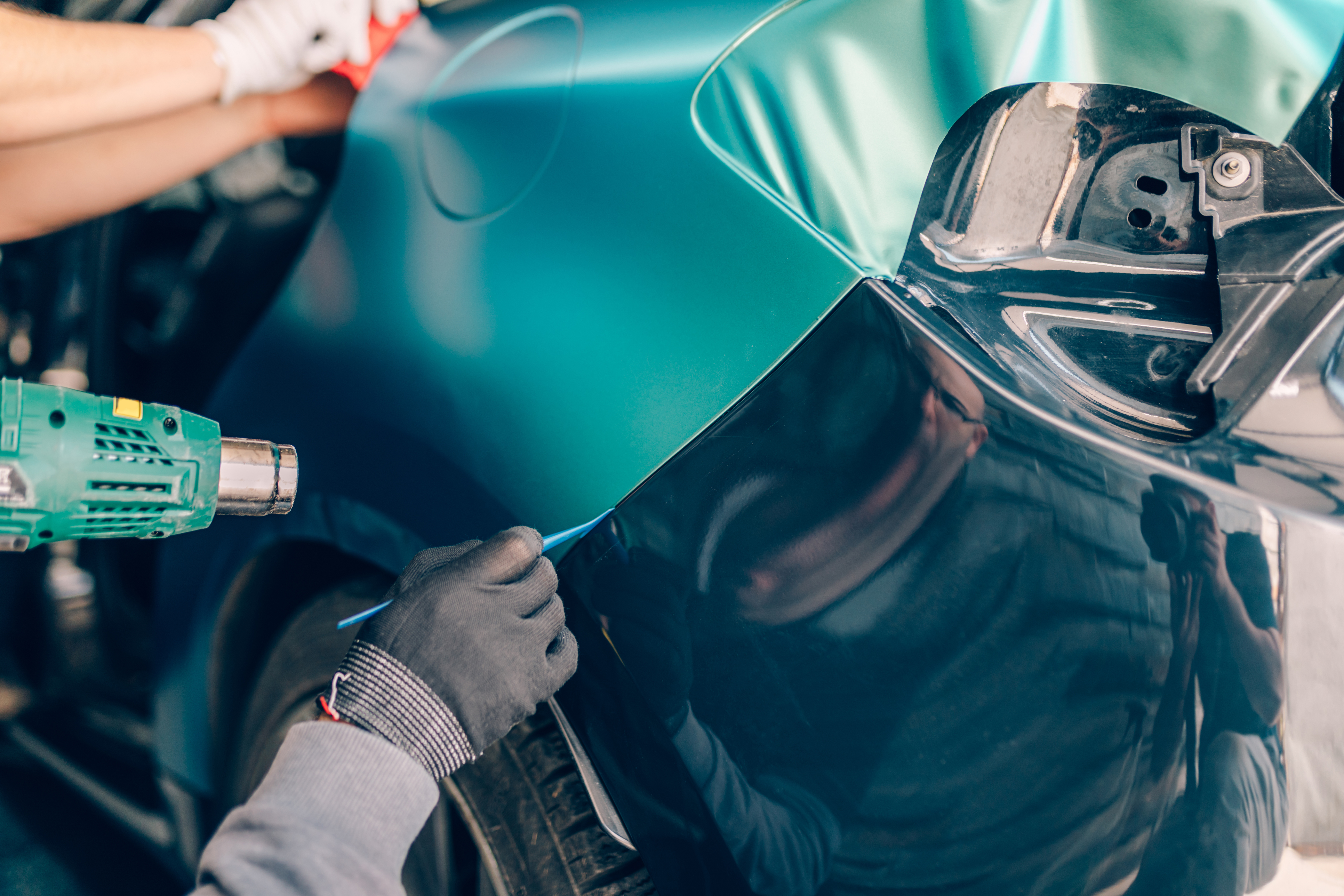
Adhesive Strength Comparison Test
This test evaluates changes in adhesive strength due to variations in tape composition (single-sided or double-sided thin film) and film thickness. Test results show that SK Dyne™ 1515DT has higher adhesive strength than general products when varying tape composition and film thickness. In addition, the 15 µm thickness SK Dyne™ 1515DT achieved the same strength as the 50 µm thickness of the general product.
It maintains strong adhesive strength even with thin films, and exhibits high adhesion to adherends such as stainless steel, glass, polycarbonate, and acrylics.
- ●Test conditions
- Adherend: Stainless steel (SUS)
Sample width: 25 mm
Sample composition: 2 μm pressure-sensitive adhesive layer / 2 μm PET core material / 2 μm pressure-sensitive adhesive layer / 6 μm PET substrate
Peel angle: 180°
Peel speed: 300 mm/min
Curing conditions: 23°C, 50% RH
One-sided
Double-sided thin film
Relationship between adhesive strength and film thickness (one-sided)
SK Dyne™ 1515DT
Expected Applications
- Securing smartphone and tablet cases and panels
- Securing parts for smartphones, wearables, and other devices
- Mounting metal and plastic nameplates
- Advertisements and bulletins
- Anchoring for flooring
Examples of electronic device applications
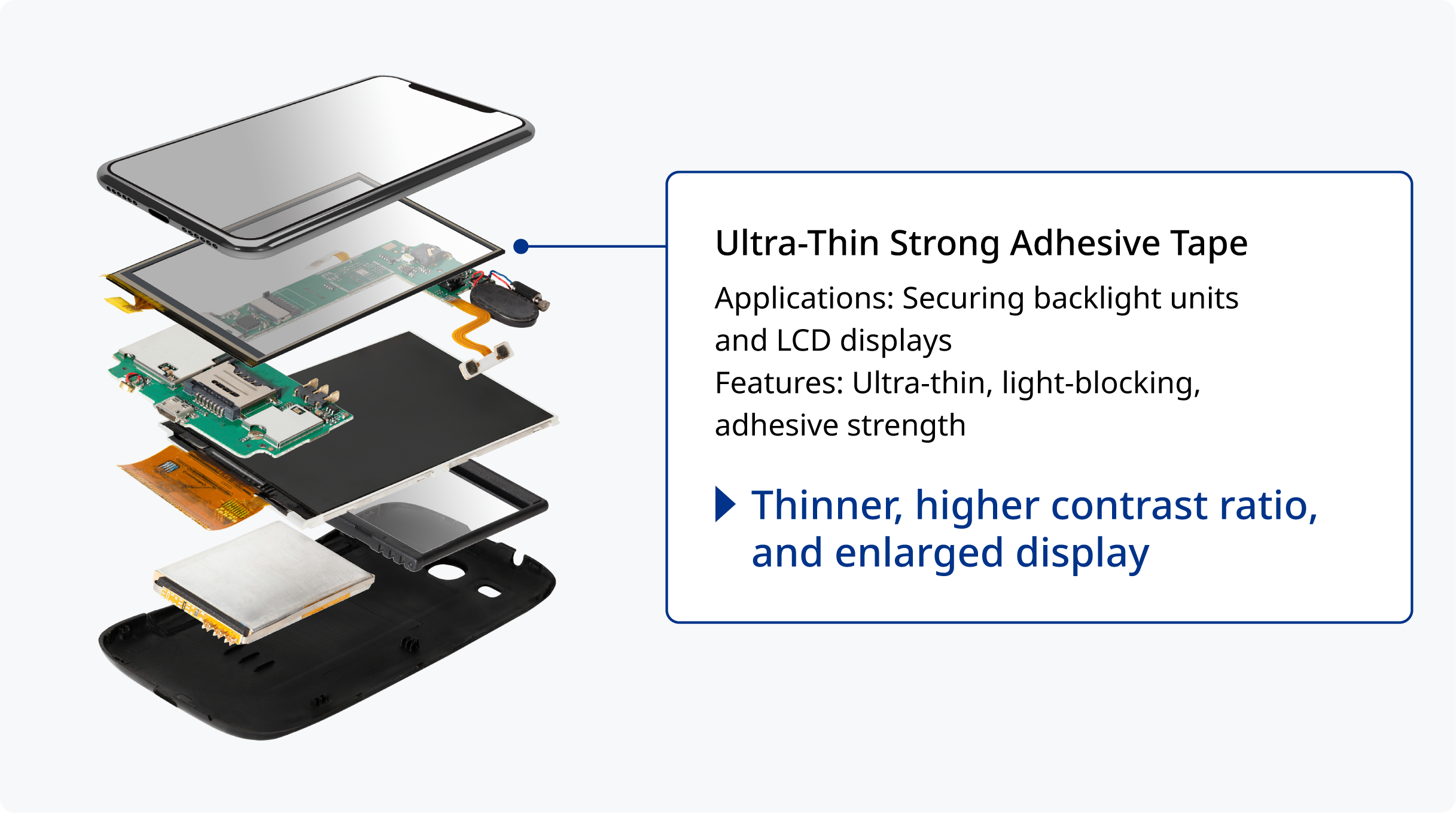
Whitening
Issue and Concerns
General pressure-sensitive adhesives are susceptible to whitening due to moisture penetration into the adhesive at high temperatures and humidity levels.
Whitening of pressure-sensitive adhesives can result in the following.
*Can be scrolled horizontally
Examples | Issue occurrence |
---|---|
Electronic displays and digital devices | Whitening occurs on screens that require transparency, resulting in defects and product failure |
Window films | Reduced visibility outside the vehicle can lead to accidents |
Process protection for optical components | It can become impossible to conduct smooth examinations, areas that are being protected can suffer negative effects, and the passing products can be judged as defective, resulting in a lower yield rate |
Causes of Whitening
Pressure-sensitive adhesives are used to stick display optics, window films, and protective adhesive films together. In hot and humid environments, such as during the rainy season and summertime, moisture can penetrate the adhesive, causing it to look whiter.
The Soken Solution
In order to eliminate this whitening effect, the product must have the ability to withstand the effects of hot, humid, and moist environments. If it is used in an electronic display, it must not affect visibility.
SK Dyne™ 1838 can suppress whitening caused by moisture and can eliminate defects caused by high temperature and humidity.
Whitening caused by heat and humidity
High humidity refers to a condition in which the amount of moisture in the air is high. Under high humidity conditions, the adhesive tape appears transparent when moisture permeates the adhesive. However, suppose it is returned to room temperature while containing moisture. In that case, the moisture will cool and clump (condense), resulting in microscopic droplets of water that form on the adhesive layer and appear white.
Heat and Humidity Whitening Test
The heat and humidity whitening test evaluates whether or not whitening occurs in the adhesive tape when it is returned to room temperature after existing in a hot and humid environment. After attaching the adhesive tape to the adherend, it is placed into a hot and humid environment. After a certain period of time, the tape is removed and returned to room temperature. After cooling to room temperature, the adhesive tape is checked for whitening with a haze meter that measures the level of cloudiness. In this test, the tape is stuck to glass and placed under high temperature and humidity for 500 hours, whereupon it is returned to normal temperature and evaluated. Temperature and humidity were set to 60°C and 90% respectively.
When ordinary adhesives are returned to room temperature from hot and humid conditions, whitening occurs due to condensation of moisture. However, SK Dyne™ 1838 remains transparent due to its resistance to whitening caused by heat and humidity.
This quality makes it suitable for a variety of products where transparency of the adhesive tape is required.
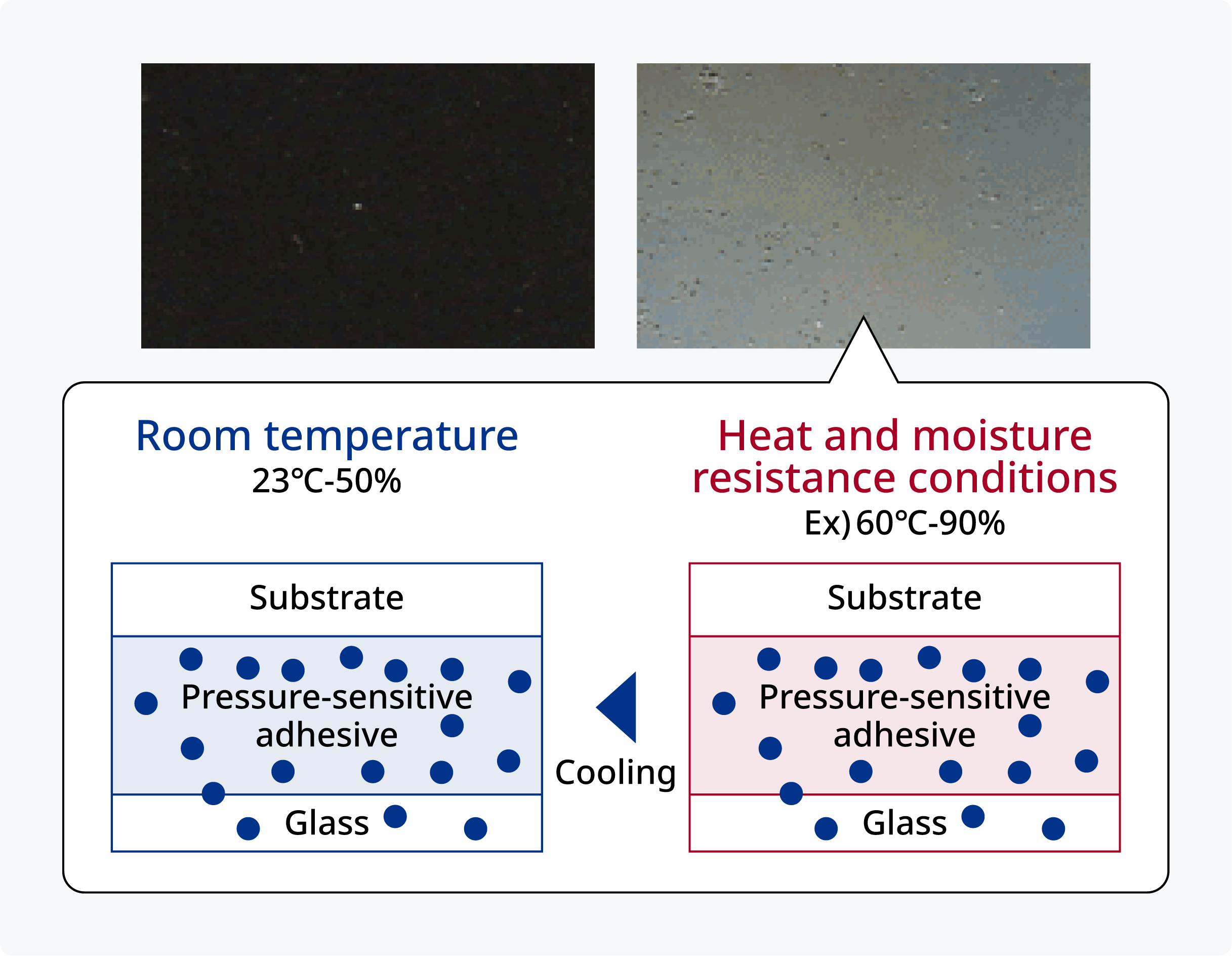
SK Dyne™ 1838
Expected Applications
- Digital devices such as smartphones and tablets
- Electronic displays like TVs and monitors ・Window films
- Laminated glass and other applications where glass is affixed to glass
- Process protection tape
- Other applications that require transparency or use in hot and humid environments
- Note: The data listed are for reference only and are not standard values.
In addition, there is no guarantee that the listed uses will not infringe on any patents.