Learn More About Other Pressure-Sensitive Adhesives
This page describes the features, applications, and advantages and disadvantages of rubber, silicone, and urethane pressure-sensitive adhesives.
Rubber Pressure-Sensitive Adhesives
Rubber pressure-sensitive adhesives stick well to a wide range of materials and are used in many different fields. Examples of everyday items that contain these adhesives include packaging tape and cellophane tape.
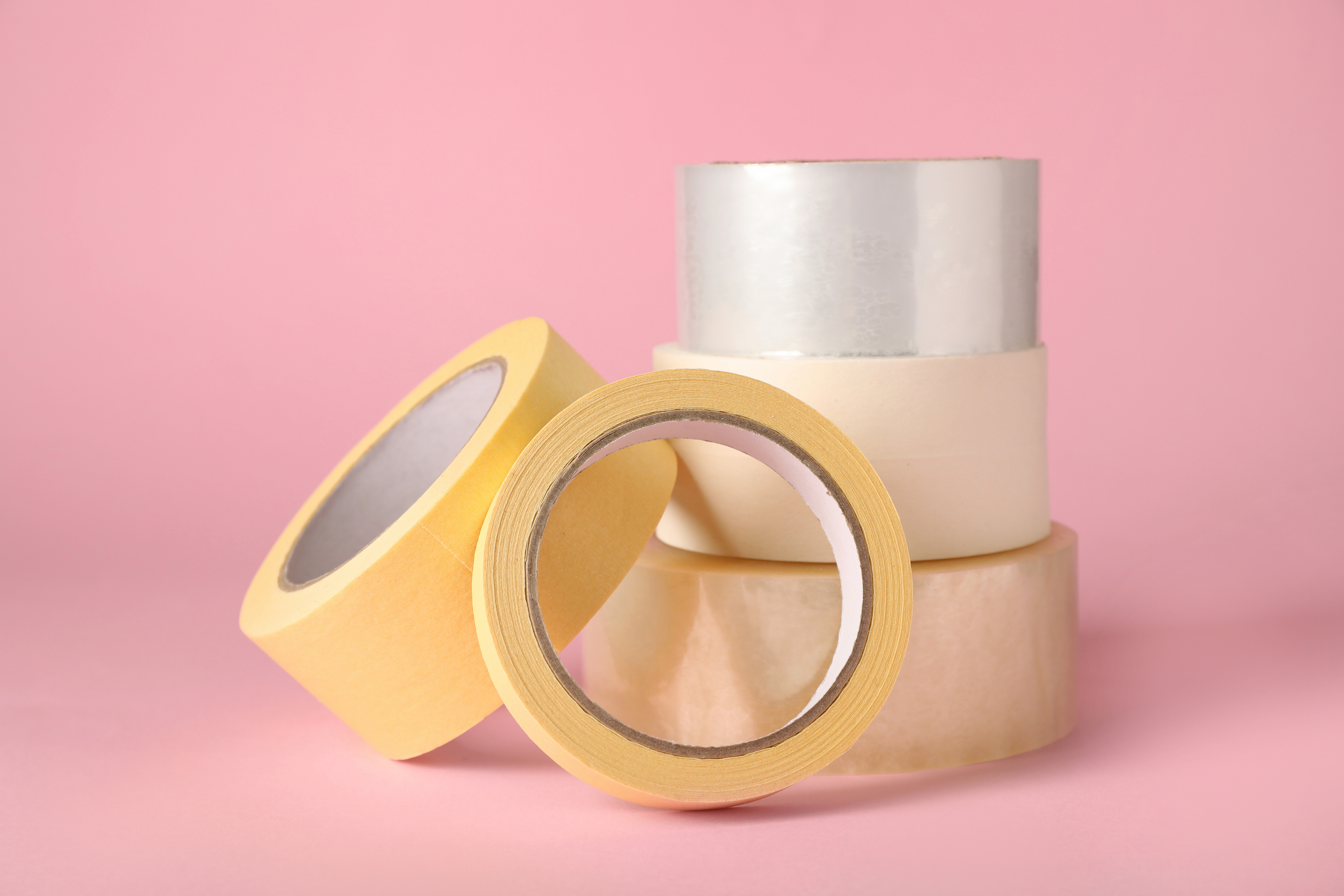
Features
The many types of rubber pressure-sensitive adhesives can be divided into two main categories: natural and synthetic. By itself, rubber exhibits no adhesive properties, and therefore does not stick to anything.
To make it adhesive, it must be mixed with resins known as tackifiers. Tackifiers have the effect of lowering the elastic modulus (or hardness) of rubber, making it softer and more adhesive so that it will stick to many different materials.
1. Natural Rubber Pressure-Sensitive Adhesives
Natural rubber is made from latex, a component of sap collected from rubber trees. Natural rubber pressure-sensitive adhesives are made by adding tackifiers and anti-aging antioxidants to latex.
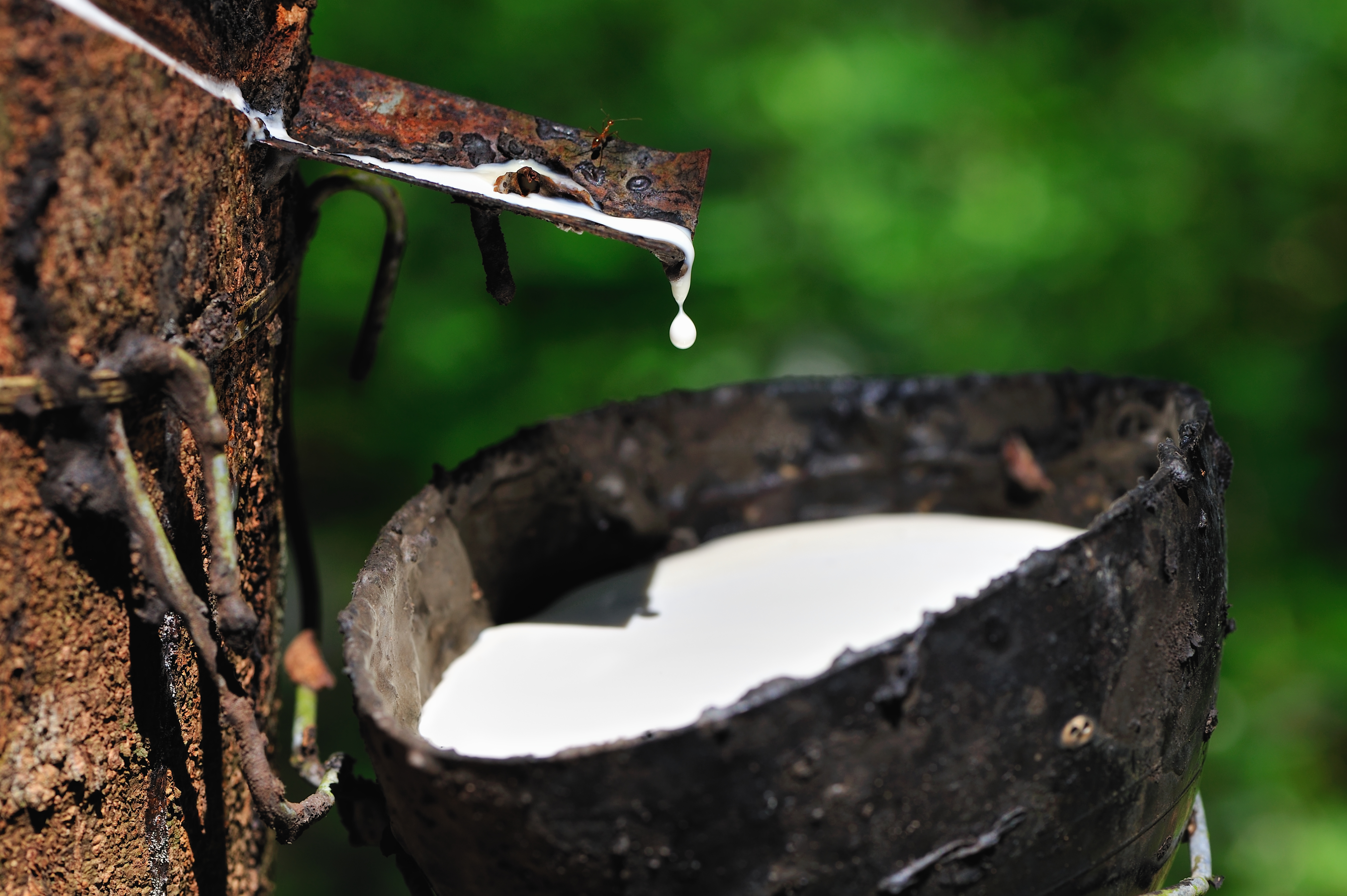
Features
Historically speaking, natural rubber pressure-sensitive adhesives made from rubber were the first adhesives ever to be used.
In its original state, natural rubber is quite hard, so it must be kneaded before anything can be done with it. This process severs and softens molecular chains, allowing us to mix in resins and additives to make the rubber sticky.
Natural rubber pressure-sensitive adhesives are highly flexible and fluid (wettable) and can stick to essentially anything.
Applications
Packaging tape, electrical tape, masking tape, protective tape, double-sided tape, kraft paper tape, and more.
2. Synthetic Rubber Pressure-Sensitive Adhesives
Synthetic rubber pressure-sensitive adhesives are made from synthetic rather than natural rubber.
Examples of synthetic rubber pressure-sensitive adhesives include styrene-butadiene rubber (SBR), polyisobutylene (PIB) rubber, styrene-isoprene-styrene block copolymers (SIS), styrene-butadiene-styrene block copolymers (SBS), styrene-ethylene-butylene-styrene block copolymers (SEBS), and styrenic block copolymers (SBC).
Features
The features of synthetic rubber pressure-sensitive adhesives can be adjusted to fit different applications and purposes. For example, the adhesives can be made harder to increase durability, or softer to augment wettability for adhering to materials.
Adjusting component ratios during synthesis and the mix proportions of tackifiers and other additives can make the adhesives more or less resistant to cold or water, transparent, elastic, or vibration-damping, to name a few performance characteristics.
Some synthetic rubber pressure-sensitive adhesives can be made into hot-melt adhesives. Block copolymer pressure-sensitive adhesives are used to form physical crosslinks called domains, which are quite cohesive. When heat is applied, the domains collapse and become fluid and soft. When the heat is removed, the domains re-form and harden. This behavior makes block copolymer pressure-sensitive adhesives ideal for hot-melt adhesives.
Synthetic rubber pressure-sensitive adhesives have many characteristics that are useful for a broad range of applications.
Applications
Packaging tape, protective tape, ordinary labels, binding tape, and more.
Advantages and Disadvantages of Rubber Pressure-Sensitive Adhesives
The advantages and disadvantages of rubber pressure-sensitive adhesives are as follows.
Advantages
- Sticks to all kinds of materials
Rubber pressure-sensitive adhesives stick well to many different materials, even when surfaces are rough or uneven. They can even be used on polypropylene, polyethylene, and other low-surface-energy, low-polarity materials that do not stick to other things well. - No preparation of coating liquid or aging required
Rubber pressure-sensitive adhesives do not need to be mixed with hardeners before coating or aged after coating. They are ready to use immediately. - Affordable
Rubber pressure-sensitive adhesives are typically less expensive than other types of adhesives. - Strong initial adhesion and high tack
Rubber pressure-sensitive adhesives exhibit adhesive strength faster than other types of adhesives. They also tend to have a strong initial stickiness. - Good adhesion at low temperatures
Rubber pressure-sensitive adhesives are highly resistant to cold—they stay fluid and stick to materials even when temperatures are low. - Excellent insulation
Rubber is an excellent insulator that can be used to prevent electric shocks.
Disadvantages
- Low durability
Rubber pressure-sensitive adhesives are not very durable. They sometimes come unstuck after long periods. - Limited design capacity
Rubber pressure-sensitive adhesives do not allow much design freedom. Sometimes, the desired specifications are out of reach. - Sensitive to sunlight
Rubber pressure-sensitive adhesives are sensitive to ultraviolet rays, making them prone to deterioration and fading when used outdoors. - Sensitive to surroundings
Rubber pressure-sensitive adhesives perform differently depending on the humidity, temperature, and other conditions of their surroundings. They also tend to soften and become less adhesive and cohesive when temperatures are high (40 to 70°C).
Acrylic pressure-sensitive adhesives are a better choice in high temperatures, outdoors, and other situations that require durability.
Silicone Pressure-Sensitive Adhesives
Silicone pressure-sensitive adhesives are highly resistant to heat, weather, chemicals, and water. They are also resistant to cold, making them useful for many applications across a broad range of temperatures.
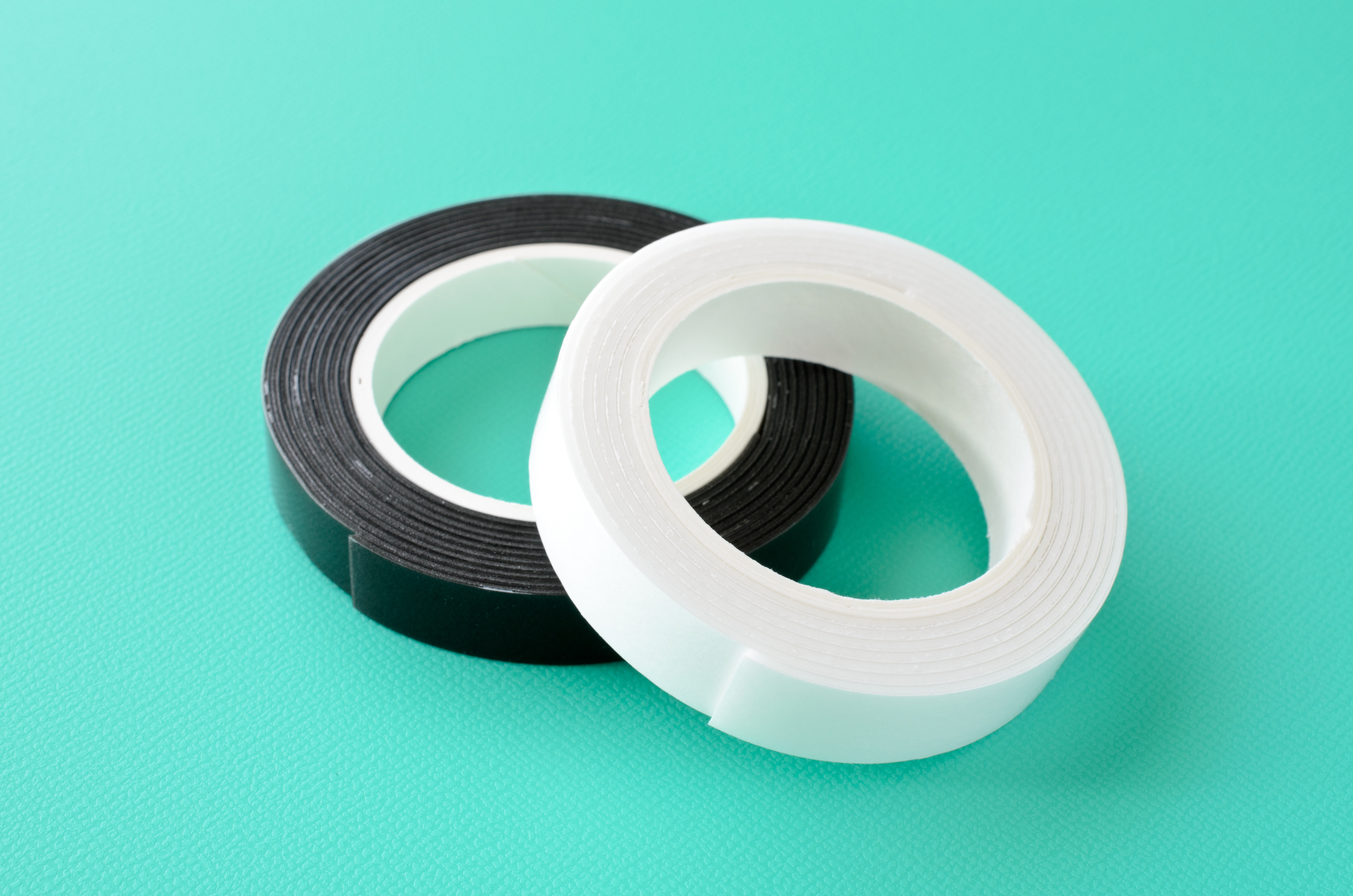
Features
Silicone pressure-sensitive adhesives comprise silicone polymers and silicone resins that serve as tackifiers.
Silicone polymers are not very adhesive, so they are mixed with silicone resins to make them stickier. The level of adhesion can be adjusted by changing the mix proportions of the polymers and resins or using different resins.
Silicone pressure-sensitive adhesives are known for being fluid and soft without being too sticky, and stick well to many different materials, including silicone rubber and fluororesins that typically do not take well to rubber and acrylic pressure-sensitive adhesives.
The mildly adhesive types used on protective films for electronic devices are excellent at releasing air, minimizing air bubble entrapment during application.
They can also be used across a broad range of temperatures (-60 to 250°C). They do not melt or harden or experience substantial changes in adhesive strength in high or low temperatures, meaning they can stick to materials even when heat is applied or temperatures are low. Silicone pressure-sensitive adhesives are ideal for medical tape because they do not stretch the skin or pull out hairs—they do not irritate the skin much when applied or hurt much when removed.
They are also resistant to water, weather, oils, chemicals, and electricity, and are waterproof. With these and other characteristics, silicone pressure-sensitive adhesives are versatile and useful for a broad range of applications.
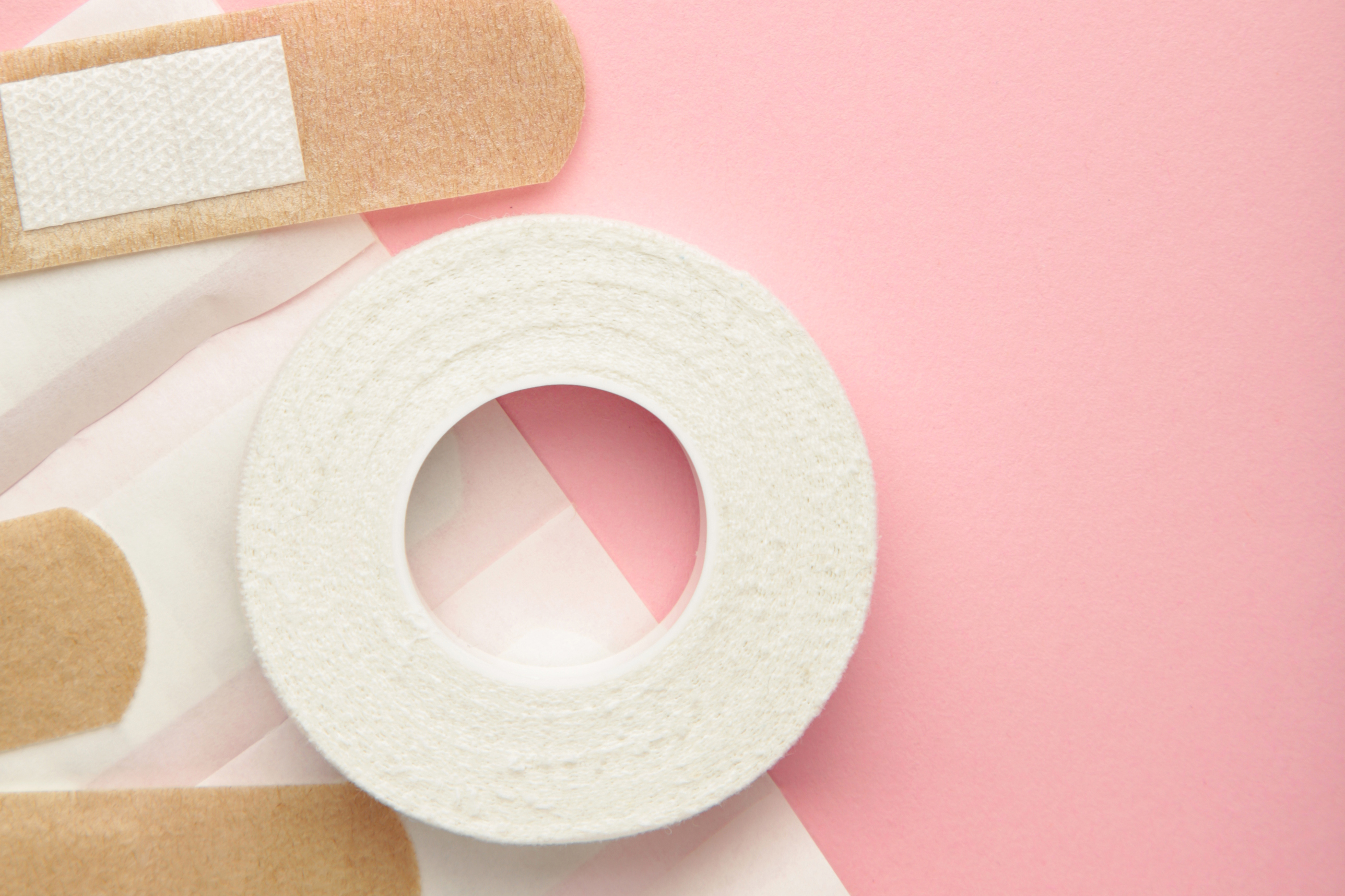
Applications
Protective film, waterproof tape, anticorrosion tape, medical tape, heat-resistant tape, electrical tape, and more.
Advantages and Disadvantages of Silicone Pressure-Sensitive Adhesives
The advantages and disadvantages of silicone pressure-sensitive adhesives are as follows.
Advantages
- Easy to remove and reapply
Silicone pressure-sensitive adhesives are very easy to remove and reapply without losing stickiness or adhesive strength. - High durability
Silicone pressure-sensitive adhesives are highly resistant not only to heat and cold, but also to ultraviolet rays, sunlight, and other elements of weather. Their physical properties essentially remain intact even in harsh climatic conditions, making them apt for use outdoors. They are used on anticorrosion tape applied to the parts of pipes exposed to the elements, pipe joints, and other areas to prevent metal corrosion. - Resistant to solvents and chemicals
Silicone pressure-sensitive adhesives resist infiltration by alcohol and other polar organic compounds. Although they swell on contact with non-polar or low-polarity compounds such as benzene and toluene, they return to normal when the solvents are removed. They are also highly resistant to oils in high temperatures (100°C or higher).
Disadvantages
- Expensive
Silicone pressure-sensitive adhesives are more expensive than other types of adhesives. - Weak adhesion
Silicone pressure-sensitive adhesives typically have low adhesive strength, making them a poor choice in situations where strong adhesion is required. - Possible adverse effects of siloxanes
Gasified siloxanes pose a risk of product defects, including contact faults in electronic components and fogging in optical components. They can also contaminate surfaces when applied in high temperatures, for example the surfaces of wafers when used on semiconductor tape.
Acrylic pressure-sensitive adhesives are a better choice when strong adhesive strength is required, or to achieve balance between price and performance.
Urethane Pressure-Sensitive Adhesives
Urethane pressure-sensitive adhesives are mildly adhesive and very easy to remove and reapply. Urethane resins are versatile and useful for a broad range of applications, including as adhesives. Their characteristics make them a suitable base for pressure-sensitive adhesives. Although urethane compounds currently lack versatility as pressure-sensitive adhesives, work is underway to add new value and develop more applications.
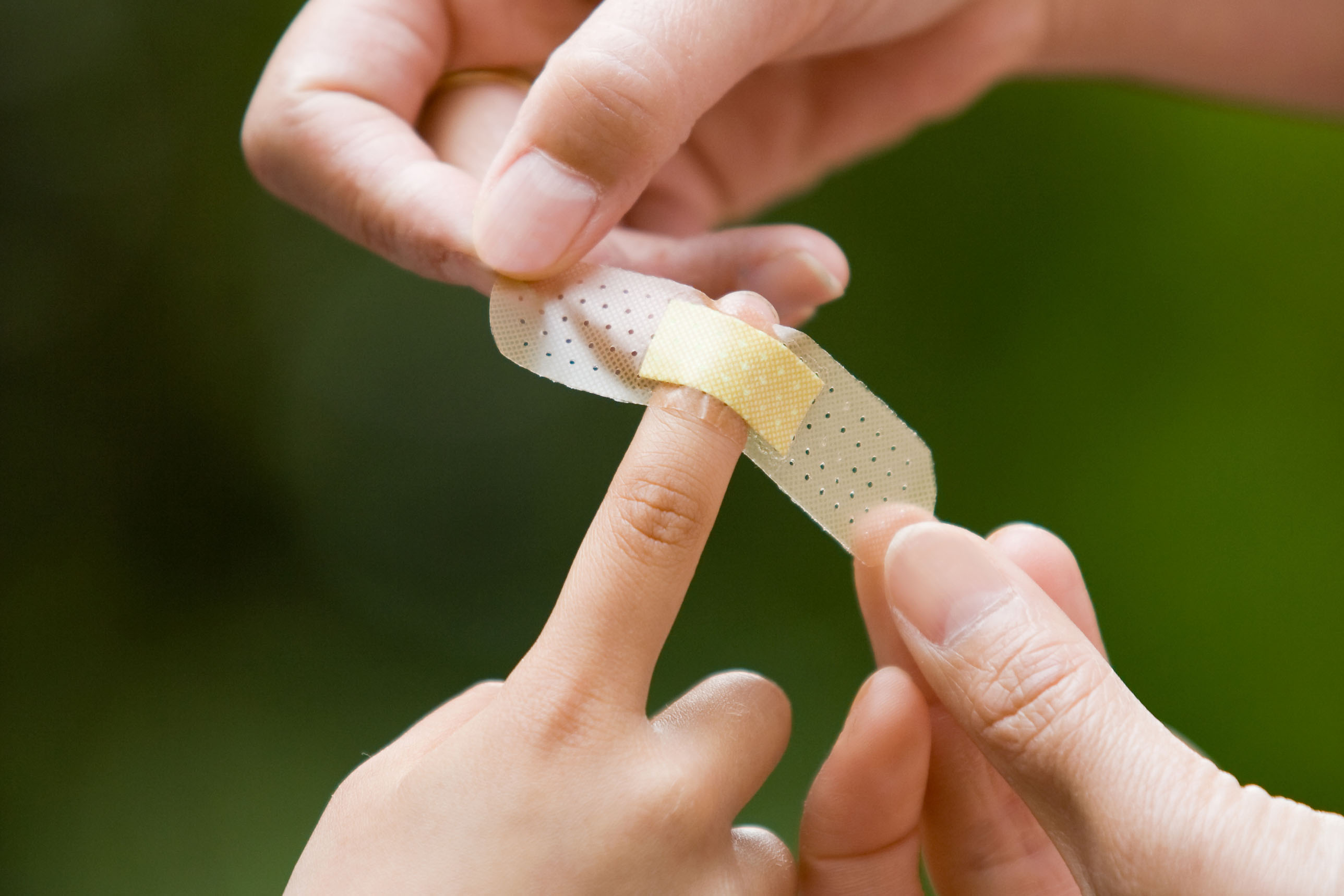
Features
Urethane pressure-sensitive adhesives are composed of polyols and polyisocyanates and contain urethane groups. They comprise high-cohesion hard segments and low-cohesion soft segments that can be adjusted to elicit and control various physical properties, including adhesion and holding power. The constituent urethane groups are highly cohesive, making urethane pressure-sensitive adhesives mildly adhesive and easy to remove and reapply. Urethane pressure-sensitive adhesives are also being used as medical tape for the strength of their other characteristics. They are highly moisture-permeable thanks to high polarity, and their properties are stable due to elasticity that is largely independent of temperature and frequency. They also give off minimal odors and cause very little skin irritation.
However, urethane pressure-sensitive adhesives require creative steps to control their hardness and molecular weight, making it somewhat impractical to develop adhesive properties for a broad range of applications. Studies are underway to solve this problem through chain extension or by introducing plasticizers to expand design freedom and improve adhesive properties. Urethane pressure-sensitive adhesives have characteristics that their rubber and acrylic counterparts do not, so if these drawbacks are resolved, we may be able to create pressure-sensitive adhesives with new added value.
Applications
Protective film, medical tape, industrial protective tape, and more.
Advantages and Disadvantages of Urethane Pressure-Sensitive Adhesives
The advantages and disadvantages of urethane pressure-sensitive adhesives are as follows.
Advantages
- Easy to remove and reapply
Urethane pressure-sensitive adhesives are easy to remove and reapply, and can be peeled off without leaving adhesive residue even if left on for long periods of time. - Low dependence on external factors
Urethane pressure-sensitive adhesives essentially maintain their adhesive strength regardless of temperature and peeling speed. Their hardness generally stays the same around room temperature, resulting in consistent adhesive strength. - High moisture permeability
Urethane pressure-sensitive adhesives are highly moisture-permeable, for example, allowing water vapor passage to reduce discomfort when applied to the skin. - Conducive to high solid differentiation
Urethane pressure-sensitive adhesives have a relatively low molecular weight, making it easy to increase the ratio of active ingredients.
Disadvantages
- Low adhesion and tack
Urethane pressure-sensitive adhesives generally have low adhesive strength and tack, making them a poor choice in situations where strong adhesion or initial adhesion are required. Also, adjusting their cohesion and degree of crosslinking to augment their adhesion reduces the strength of the pressure-sensitive adhesive layer, which may result in adhesive residue. - Will not stick to olefines
Urethane pressure-sensitive adhesives often do not stick well to low-polarity materials. - Difficult to increase molecular weight
The molecular weight of urethane pressure-sensitive adhesives cannot be increased easily, making it difficult to increase or otherwise adjust the viscosity. Doing so may also compromise the durability of the pressure-sensitive adhesive.
Acrylic pressure-sensitive adhesives are a better choice when strong adhesive strength, tack, or durability are required.
- Note: The data listed are for reference only and are not standard values.
In addition, there is no guarantee that the listed uses will not infringe on any patents.