Learn More About Acrylic Pressure-Sensitive Adhesives
Acrylic pressure-sensitive adhesives have excellent transparency, weather resistance, and heat resistance. The wide range of raw materials available, coupled with the ability to modify molecular weight during the polymerization process, enables the design of adhesives tailored to desired properties. This high degree of versatility has led to their widespread use in the tapes we encounter every day. This page describes the characteristics, applications, advantages, and disadvantages of acrylic adhesives.
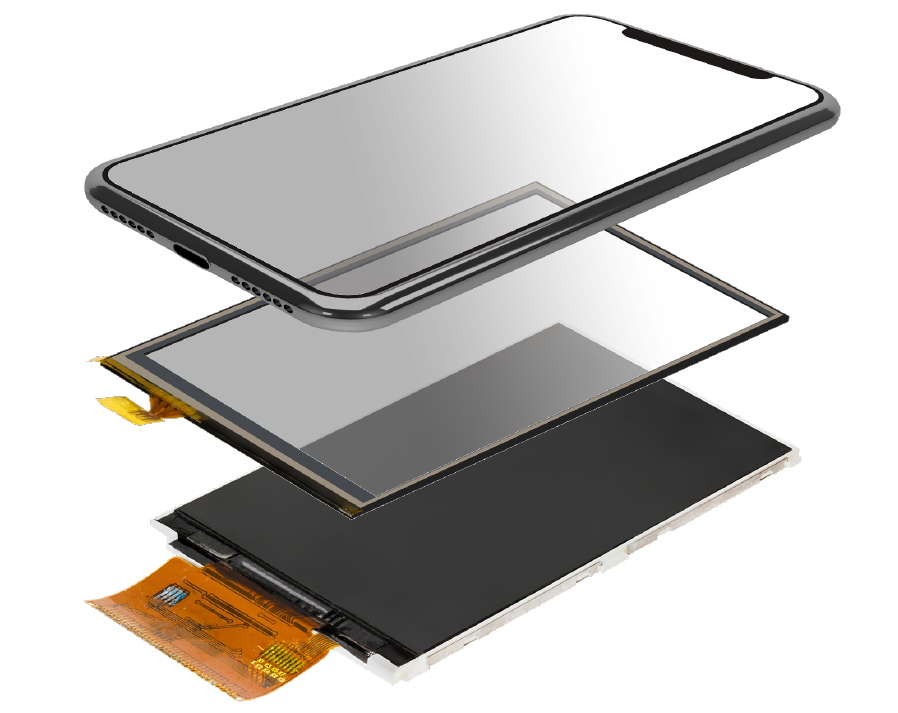
Characteristics of Acrylic Pressure-Sensitive Adhesives
Acrylic pressure-sensitive adhesives are synthesized with acrylic acid ester as the main ingredient. There are many different kinds of acrylic acid esters, and with the proper design techniques, they can be utilized to make pressure-sensitive adhesives suited for a wide variety of purposes. Their broad range from strong to weak adhesion allows their use in a diverse set of applications, from permanent mounting tapes, to those designed for temporary protection and quick detachment.
Pressure-sensitive adhesives made from rubber or silicone require components such as tackifying resins (tackifiers) to adjust adhesion strength, while acrylic pressure-sensitive adhesives are inherently adhesive and readily stick to various materials. Though the primary ingredient is adhesive, it struggles to stick to substrates with low polarity and low surface energy, such as polypropylene, particularly under cold conditions. To alleviate these shortcomings, it's sometimes necessary to blend in resins that enhance adhesion. There are three types of acrylic adhesives: solvent-based, emulsion, and solvent-free.
Solvent Acrylic Pressure-Sensitive Adhesives
Solvent acrylic pressure-sensitive adhesives are made by dissolving acrylic ester copolymers, and in some cases additives such as tackifying resins, in organic solvents, which are then volatilized to leave behind the material with adhesive properties. These materials are generally synthesized in solution via radical polymerization, and their adhesive properties are adjusted by changing their Tg (glass transition temperature), molecular weight, and molecular weight distribution. Solvent-based acrylic pressure-sensitive adhesives have excellent resistance to heat and weather, and their adhesive properties remain stable over long periods of time.
Functional groups are introduced into the polymer component, and a curing agent (cross-linking agent) is used to further improve adhesive properties. A wide variety of curing agents are available, chosen according to the desired properties. Furthermore, by varying the amount of solvent, it is relatively easy to adjust the amount of solid content and the viscosity, allowing for treatment of various thicknesses, including thin film coatings of 5 to 10 μm. However, the inclusion of solvents raises concerns about flammability risks and the potential harmful impacts of volatile organic compounds on both people and the environment. When using these materials, considerations must be given to proper safety management of the work area, such as adequate ventilation and other protective measures.
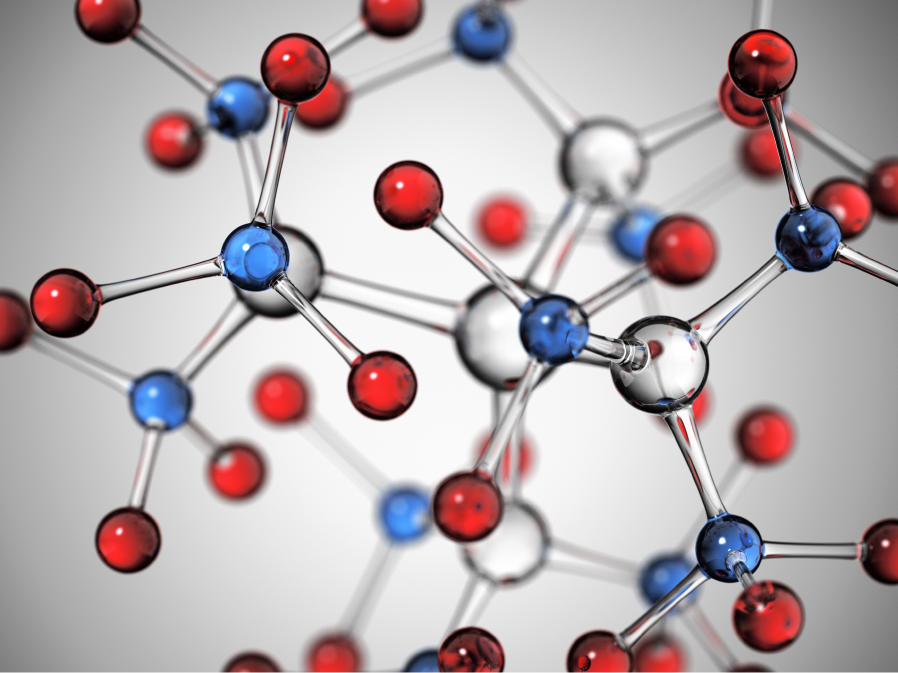
Emulsion Acrylic Pressure-Sensitive Adhesives
Emulsion acrylic pressure-sensitive adhesives are materials in which the adhesive component is dispersed in water. These pressure-sensitive adhesives use water instead of organic solvents, so they are considered safe and environmentally friendly. Primarily synthesized through emulsion polymerization, these adhesives facilitate high molecular weight due to reactions occurring within dispersed particles in water, resulting in polymers with high cohesion, inclusive of gel fractions (components insoluble in solvents). Therefore, single-component designs without a curing agent are also possible.
On the other hand, because non-adhesive components such as emulsifiers (surfactants) and preservatives are used, water resistance, moisture resistance, and other adhesion-related properties are often inferior to solvent-based materials. In addition, not many types of tackifying resins can be used with these materials, so there is not much room for performance adjustment. Furthermore, compared to solvent-based materials, these materials have worse drying efficiency and are associated with concerns of decreased productivity, so mitigating strategies need to be considered.
Solvent-Free Acrylic Pressure-Sensitive Adhesives
Solvent-free acrylic pressure-sensitive adhesives are materials with 100% active ingredients that cure by UV light. Similar to emulsion adhesives, they do not use solvents and have a minimal environmental impact. Moreover, without volatile components, it is possible to form a thick adhesive film with a single application. UV-polymerized types and UV crosslinked types are available. Among them, UV-polymerized types allow for high polymer formation, greater freedom in molecular design, and improved heat resistance and durability.
Since these solvent-free materials cure via ultraviolet light, various curing conditions such as the type of UV lamp and the amount of radiation are also important factors. In addition, since these materials require dedicated equipment, the cost of installation must also be taken into consideration. Furthermore, it should be noted that residual unreacted monomers can cause strong, foul odors.
Applications
Protective films, optical films, curingtapes, double-sided tapes, foam tapes, part-fastening tapes, general-use labels, food labels, and more.
Advantages and Disadvantages of Acrylic Pressure-Sensitive Adhesives
The advantages and disadvantages of acrylic pressure-sensitive adhesives are as follows.
Advantages
- High degree of design versatility
With a rich variety of raw materials such as acrylate esters, tackifying resins, and curing agents, and the ability to adjust from low to high molecular weight through controlling the polymerization, it is possible to design with targeted properties in mind. - Ease of adhesive strength modification
These materials, capable of being tailored for both strong and weak adhesion, are versatile enough for uses requiring enduring bonds as well as for applications where removal is necessary. - High resistance to weather
These materials are not easily affected by natural environmental factors such as sunlight, temperature, humidity, and rain, and thus are suitable for use outdoors. - High transparency
These materials have excellent transparency and do not readily discolor. Suitable for use where transparency is required, such as in optical applications. - Strong adhesion to metal
These materials have good compatibility with various metal substrates such as iron and aluminum and exhibit excellent adhesive properties.
Disadvantages
- Low adhesion to plastics
Due to their high polarity, these materials have difficulty adhering to hard-to-adhere materials with low polarity and low surface energy, such as polypropylene. - Poor adhesion in low-temperature environments
Due to the effects of Tg, fluidity decreases in low-temperature environments, reducing stickiness and negatively affecting adhesion. - Expensive compared to rubber pressure-sensitive adhesives
Acrylic materials are more expensive compared to rubber pressure-sensitive adhesives.
Acrylic pressure-sensitive adhesives are recommended for applications that require heat resistance, weather resistance, and transparency. In addition, acrylic pressure-sensitive adhesives offer a good balance of price and performance as well as a wide range of design options, making it possible to provide adhesives that meet your requirements.
- Note: The data listed are for reference only and are not standard values.
In addition, there is no guarantee that the listed uses will not infringe on any patents.